When Dermody Properties announced its first tenant in September for the massive logistics campus supplanting the former Allstate headquarters along I-294, only one of five warehouse buildings planned for the first phase had taken shape.
Seven months later, all five buildings are nearing completion, rising up amid the mounds of dirt and towering construction equipment on the northern end of the expansive Glenview site.
But the first tenant, Upside Foods, remains the only one. And the startup cultivated meat producer, whose arrival was heralded by everyone from Gov. J.B. Pritzker to U.S. Sen. Dick Durbin, has put plans to build its first large-scale factory on hold.
The slower-than-expected start for the $500 million project, one of the largest urban logistics developments in the U.S., may reflect both waning post-pandemic demand for warehouse space and perhaps an overly optimistic bet on when lab-grown chicken would be ready to land on your kitchen table.
In October 2022, Allstate sold its longtime north suburban corporate campus for $232 million to Dermody Properties. The Nevada-based developer is turning the 232-acre property, which was annexed by Glenview, into a 10-building, 3.2 million-square-foot industrial park dubbed The Logistics Campus.
The insurance giant’s buildings and iconic Allstate sign, a familiar Tri-State Tollway landmark for more than half a century, are gone. Now hulking, low-slung warehouses loom large, with clean facades broken up by docking bays, a few windows and temporary signs advertising space available. Lots of space.
Dermody has more than 1 million square feet of warehouse space available, not including the Upside lease, which is still active, according to Neal Driscoll, Midwest region partner at Dermody. The first phase of the project is set to be completed in June.
“We have probably 800,000 or 900,000 square feet of proposals out right now,” Driscoll said. “So we feel pretty good about where we stand in the process.”
Catalyzed by remote working, supply chain issues and other pandemic trends, Chicago has become a hotspot for the development of data and logistics centers, filling the void left by the demise of sprawling corporate campuses like Allstate and Sears.
But the post-pandemic demand for industrial properties has slowed, just as some of those developments, including the Dermody logistics site, are set to come online.
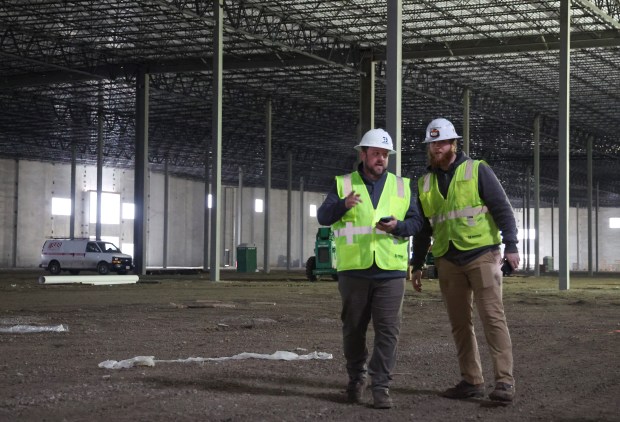
Commercial real estate company Transwestern reported industrial market conditions in Chicago softened last year, with leasing activity down by 39% and available sublease space increasing by 40%. Meanwhile, the amount of construction starts declined by 50% year-over-year, according to the report.
Driscoll said many companies that committed to rapid logistics expansion during the supply chain bottlenecks of the pandemic have taken their foot off the gas to “be more strategic” in the uncertainty of the post-COVID economy. The slowdown in leasing activity, he said, reflects that caution.
“Even though the market overall has cooled a little bit, it doesn’t cause us any concern, because the reality is we’re just sort of reverting back to what the norm was pre-COVID demand,” Driscoll said.
While warehouses abound in southwest suburban Joliet and other communities along the I-55 freight corridor, the Glenview Logistics Campus is breaking new ground in the northern suburbs, which Driscoll hopes will set it apart in the potentially overbuilt Chicago market.
As to its only tenant, California-based Upside Foods, which signed a long-term lease for 187,000 square feet to build out the first large-scale cultivated meat plant in the U.S. by next year, those plans were put on hold in February, with no target date for launch.
Announced with great fanfare in September, Upside said it would invest $140 million in the facility and create at least 75 new jobs, from warehousing and logistics to food production. Upside was expected to begin operations at the new plant, dubbed “Rubicon,” in 2025.
Instead, it will “significantly expand” its smaller California production facility, known as “EPIC,” before building out and launching large-scale operations in Glenview, the company announced.
“In the process of planning for Rubicon, we identified a more efficient and cost-effective way to achieve a similar capacity and timeline of the initial phase of Rubicon by significantly expanding our operations at EPIC,” an Upside spokesperson said in an email. “We still plan to move forward with building out our full-scale commercial facility in the future.”
Upside declined to comment further.
Last fall, Pritzker topped a long list of political leaders touting the arrival of Upside, one of two food tech companies to receive approval from the U.S. Department of Agriculture in June to begin selling cultivated chicken products.
Upside was in line to receive about $15 million in Illinois grants, loans and tax credits, part of which is drawn from a new provision for startups in the state’s Economic Development for a Growing Economy program.
But the company will not receive any grants or incentives if it doesn’t follow through with its development commitments in Glenview, Department of Commerce & Economic Opportunity spokesperson Emily Bolton said.
Founded in 2015, Upside is a pioneer in the production of cultivated meat, which involves growing meat, poultry and seafood directly from animal cells. Chicken, for example, can be grown from fertilized egg cells that are fed nutrients and then multiply. The larger the size of the cultivators, the more meat that can be grown.
The Glenview facility was designed to house massive cultivators with capacities of up to 100,000 liters, making it one of the largest cultivated meat production facilities in the world, the company said. It would have an initial capacity to produce millions of pounds of cultivated meat per year, with the potential to increase its output to more than 30 million pounds annually, the company said.
Upside had planned to begin ramping up production next year.
The decision to pause its Glenview plant comes amid broader challenges facing the cultivated meat industry, including a slowdown in venture capital funding, according to analysts.
Stephanie Lind, founder and chief strategy officer of Elohi Strategic Advisors, a Chicago-based food service consultancy, said investment in the lab-grown meat space is drying up, and that it may be five years or more before the products start rolling out on store shelves. With tighter financing, companies like Upside need to extend the runway to make it to market, she said.
“I think they made the right decision for where things are right now,” Lind said. “Without funds, without the investment, they can’t build the plant, without the plant they can’t produce at scale.”
Cultivated meat is the latest innovation in the alternative protein segment, which has gained significant traction in recent years with new products such as plant-based burgers from Beyond Meat and Impossible Foods.
But demand for faux meat has stalled amid rising prices, tighter food budgets and “weakening consumer engagement,” according to a report by the Good Food Institute, a 7-year-old nonprofit promoting alternative proteins.
The plant-based food market in the U.S. — which includes everything from veggie burgers to almond milk — grew from $3.9 billion in 2017 to $8.2 billion in 2022. But sales fell slightly last year to $8.1 billion in a “more challenging market environment,” according to the report.
Sales of plant-based meat and seafood products, a subset of the broader category, grew from $682 million in 2017 to more than $1.4 billion in 2022, but fell 12% last year to $1.24 billion. For the market to grow, plant-based meat needs to taste better and cost less, the study concluded.
While there is no industry sales data yet for the nascent cultivated meat category, which arrived at two U.S. restaurants for sample taste testings last year, it has the potential to “transform protein production,” the Good Food Institute said.
Last year, both Upside and California-based Good Meat received regulatory approval to begin selling cultivated chicken products in the U.S. Upside debuted its product last summer at Bar Crenn in San Francisco, while Good Meat was offered by celebrity chef José Andrés at his China Chilcano restaurant in Washington, D.C.
Good Meat has since paused the launch of a new production facility amid a tighter fundraising market.
“It’s been a challenge for private companies that are actually building things not in AI,” said Josh Tetrick, 44, co-founder and CEO of Good Meat. “So we are a part of that challenge.”
Good Meat has nearly completed a $61 million pilot plant in Singapore that would be used to produce a low volume of cultivated meat. Previously, the company has used a contract manufacturer for trial runs in Singapore, the first country to approve the sale of cultivated meat in 2020.
The company has a research facility in California where it developed the product and likewise employed a contract manufacturer for its U.S. debut in July.
Both the U.S. and Singapore production facilities are small scale, Tetrick said.
“We have the largest installed capacity relative to anyone else in the industry,” Tetrick said. “But that’s not really saying a lot, because we have hardly any installed capacity.”
Eat Just, the parent company of Good Meat, has raised $800 million, $200 million of which is for cultivated meat development. Their leading product, Just Egg — a plant-based egg substitute — was introduced in 2019 and is in widespread distribution at grocery stores, with “tens of millions of dollars” in annual sales, Tetrick said.
Produced at a Minnesota factory, Just Egg uses mung bean protein, which can be scrambled like eggs into a vegan alternative for the breakfast plate.
Getting cultivated meat products to large-scale production likely won’t happen before the end of the decade, Tetrick said. That may not bode well for the imminent buildout of the Upside Foods plant in Glenview.
A recent visit to the Glenview site revealed a work in progress, where cavernous buildings are in various stages of completion. Leading the pack is Building 5, a 295,000-square-foot warehouse along I-294 south of Willow Road that is fully enclosed, with a concrete floor stretching three football fields long.
Workers at the adjacent Building 3 were navigating the expansive dirt floor of the unfinished 326,000-square-foot warehouse along Sanders Road, installing conduit on the towering ceiling with a lone scissor lift.
Meanwhile, Building 1 on the west side of Sanders Road, which is mostly leased out to Upside Foods, remains unfinished, with an open roof and dirt floor evoking an industrial Roman Colosseum. But it too will be fully enclosed and ready for occupancy by June, even if Upside Foods is not, Driscoll said.
“We’ll finish it up and they can decide what they want to do long term,” Driscoll said.